3rd December 2024 • 10 minute read
How do material properties impact product performance?
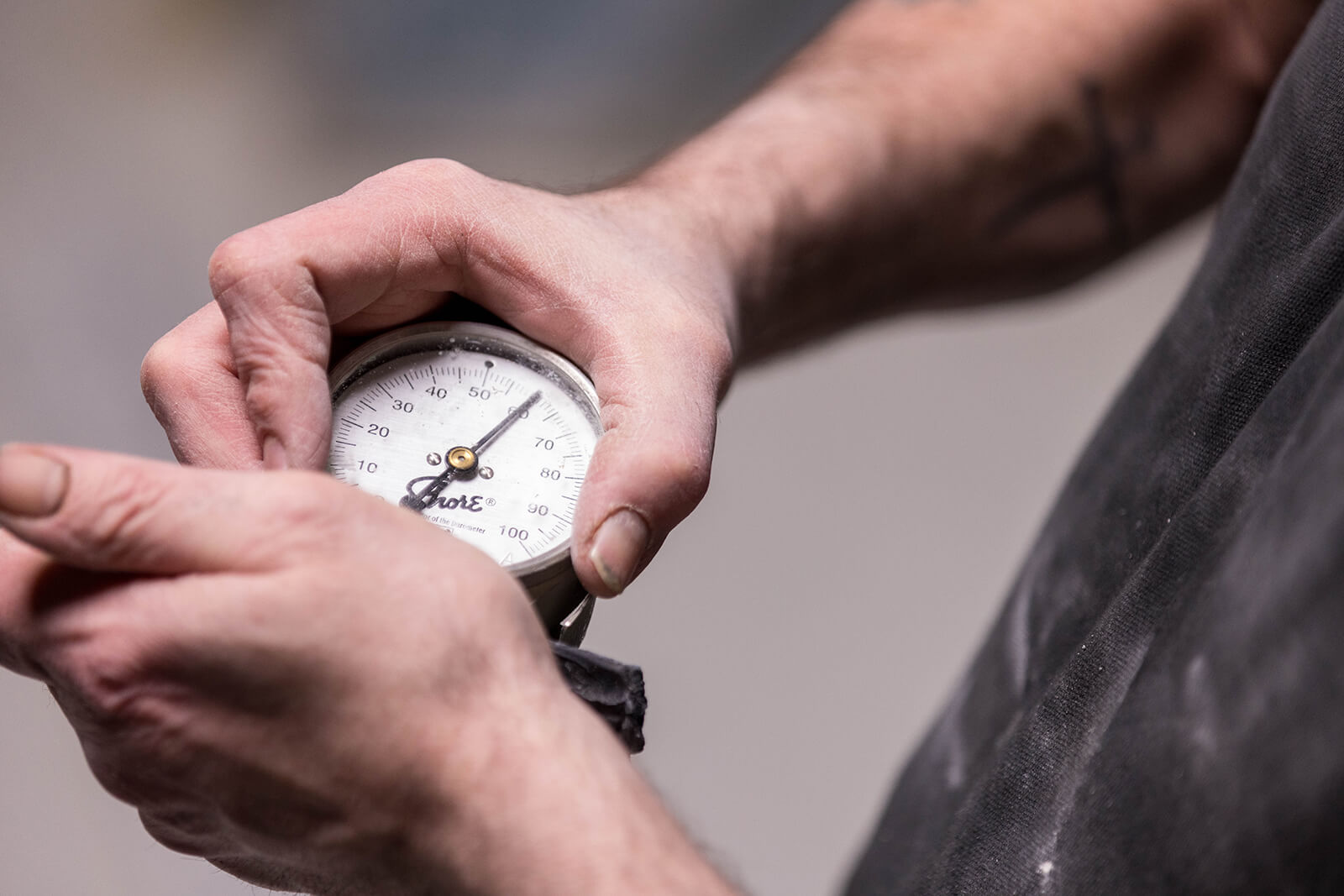
When selecting materials for rubber components, understanding how different compounds perform in specific applications is critical. Materials like EPDM, FKM (Viton®), and VMQ each have unique properties that make them ideal for certain environments, industries, and challenges. At Harltex, our in house Rubber Technologist can provide bespoke rubber solutions tailored to your exact requirements, leveraging decades of expertise in material selection and manufacturing precision.
In this blog, we explore how the properties of EPDM, FKM, and VMQ impact product performance and help you choose the right material for your applications.
Understanding EPDM: A Versatile Workhorse
Ethylene Propylene Diene Monomer (EPDM) is one of the most widely used rubber compounds due to its excellent durability and versatility.
Key Properties of EPDM:
- Weather Resistance: Exceptional resistance to UV light, ozone, and extreme weather conditions.
- Temperature Tolerance: Performs well in temperatures ranging from -40°C to 150°C.
- Water and Steam Resistance: Ideal for applications involving water or steam exposure.
- Chemical Resistance: Resists mild acids, alkalis, and some organic solvents.
Applications of EPDM:
- Automotive: Weatherstripping, hoses, and seals for doors and windows.
- Utilities: Seals for drinking water and wastewater systems.
- Construction: Gaskets and profiles for building envelopes and glazing.
Performance Impact:
EPDM’s flexibility and durability make it an excellent choice for outdoor and high-moisture applications. However, it is not suitable for environments with exposure to oils or hydrocarbons.
Exploring FKM (Viton®): The Specialist in Extreme Conditions
Fluoroelastomer (FKM), commonly known by its trade name Viton®, is a high-performance material designed for demanding environments.
Key Properties of FKM:
- Chemical Resistance: Excellent resistance to oils, fuels, and a wide range of aggressive chemicals.
- High-Temperature Performance: Operates effectively in temperatures up to 200°C.
- Low Permeability: Offers superior sealing capabilities in gas and fluid systems.
Applications of FKM:
- Automotive: Fuel system seals and gaskets.
- Industrial: Chemical-resistant seals for equipment in harsh environments.
- Aerospace: High-performance O-rings and gaskets for aviation systems.
Performance Impact:
FKM’s resistance to heat, chemicals, and pressure ensures reliability in critical systems. However, its higher cost may limit its use to applications where extreme performance is essential.
VMQ – Silicone: The Specialist in Flexibility and Hygiene
Silicone rubber stands out for its flexibility and suitability for hygienic environments.
Key Properties of Silicone:
- Temperature Range: Performs across an extensive range, from -60°C to 230°C.
- Inert and Non-Toxic: Safe for use in food, pharmaceutical, and medical applications.
- UV and Ozone Resistance: Excellent for outdoor and high-UV applications.
Applications of Silicone:
- Automotive : Seals and Hoses for extreme temperature conditions.
- Food Processing: Seals, Gaskets, Tubing and Profiles for hygienic equipment.
- Electrical: Insulating components for high-voltage applications.
Performance Impact:
Silicone excels in environments requiring flexibility, cleanliness, and thermal stability. Its higher cost and lower abrasion resistance make it less suitable for heavy-duty mechanical applications.
Choosing the Right Material for Your Application
Selecting the right material involves evaluating the operational conditions, such as:
- Temperature Extremes: EPDM is great for moderate heat; FKM and silicone excel in high-temperature environments.
- Chemical Exposure: FKM outperforms EPDM and silicone in aggressive chemical settings.
- Flexibility and Hygiene: Silicone is the go-to choice for clean-room and hygienic applications.
- Environmental Resistance: EPDM is the cost-effective weather-resistant option for prolonged outdoor use.
At Harltex, we work closely with your team to assess your requirements and recommend the optimal material for your application.
Harltex’s Expertise in Material Selection
With decades of experience in manufacturing high-performance rubber components, Harltex provides tailored solutions across industries such as automotive, marine, utilities, and healthcare. Our expertise in materials like EPDM, FKM, and VMQ ensures that your products perform reliably in the most demanding conditions.
Contact Harltex for Material Expertise and Precision Solutions
Choosing the right material is key to maximising the performance and lifespan of your rubber components. At Harltex, we deliver bespoke solutions backed by technical expertise and cutting-edge manufacturing.
Get in touch with our team today to discuss your requirements and discover how Harltex can help you achieve superior performance with precision-engineered rubber products.
Share this story
The latest news from Harltex
Building the foundations with our ISO 9001 Accreditation
At Harltex, our dedication to precision, quality, and innovation has been the cornerstone of our success since 1985. As we continue to evolve, we recognise the importance of a digital presence ...
Introducing the new Harltex.co.uk
At Harltex, our dedication to precision, quality, and innovation has been the cornerstone of our success since 1985. As we continue to evolve, we recognise the importance of a digital presence ...
Understanding the Importance of Material Selection in Rubber Manufacturing
In the world of rubber manufacturing, material selection is one of the most critical factors in ensuring the performance, durability, and reliability of finished products ...