7th January 2025 β’ 14 minute read
What is the difference between Hot feed and Cold feed extrusion?
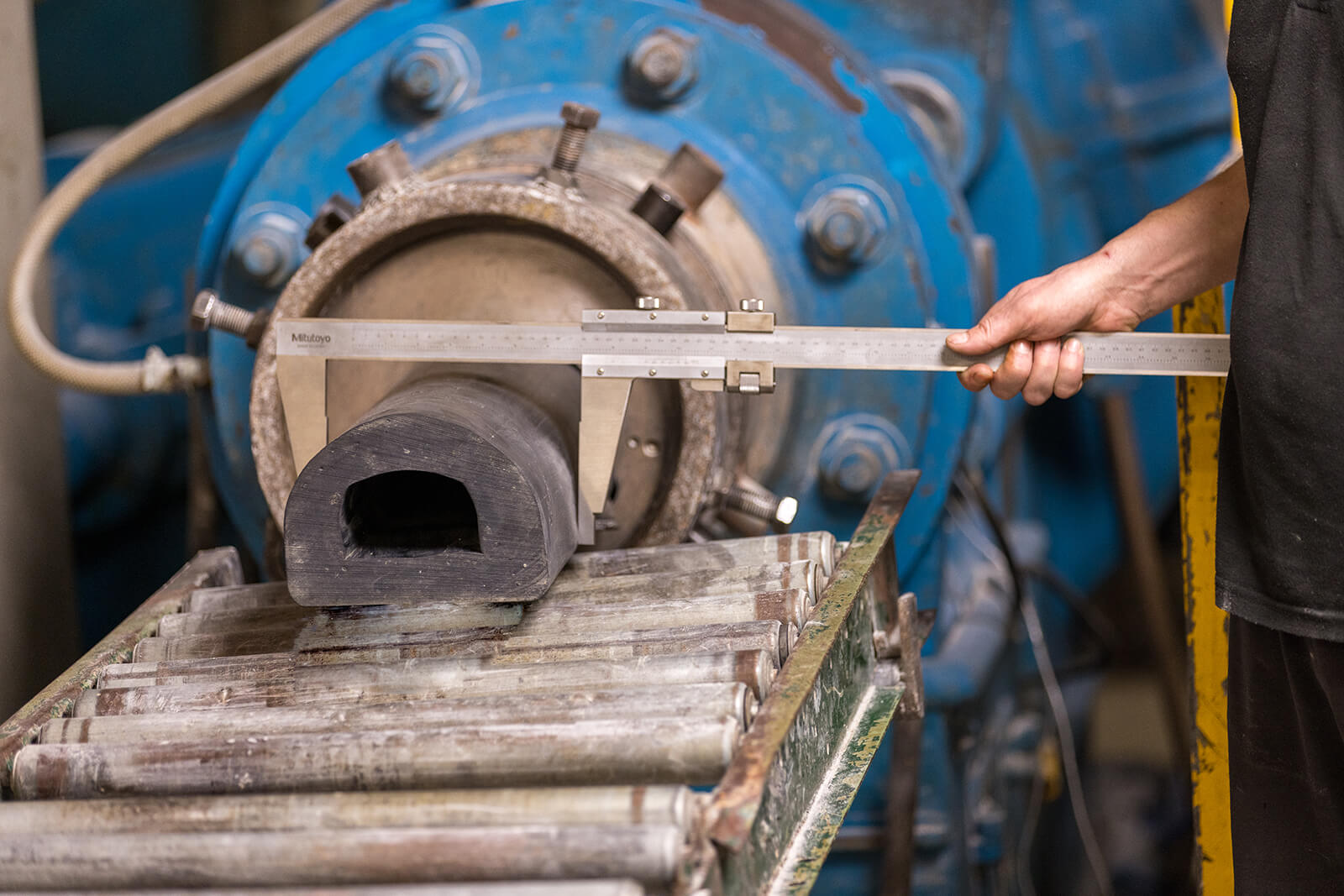
In rubber manufacturing, precision and performance rely heavily on the extrusion process. At Harltex, our expertise in both hot feed and cold feed rubber extrusion ensures we deliver tailored solutions that meet the most exacting requirements across industries, including automotive, marine, construction, and industrial sectors. But what exactly is the difference between these two processes, and which is best suited for your application?
In this blog, weβll explore the differences between hot feed extrusion and cold feed extrusion, their advantages, and where each process excels.
What is Rubber Extrusion?
Rubber extrusion is the process of forcing uncured rubber through a die to create continuous profiles with a specific cross-sectional shape. These profiles are then cured to solidify the rubber, making it suitable for its intended application.
The extrusion process is categorised into hot feed and cold feed, depending on how the rubber is prepared before it enters the extruder.
Hot Feed Rubber Extrusion
Hot feed extrusion involves pre-heated, soft rubber that is fed into the extruder. The rubber is typically warmed to around 90-120Β°C before processing, making it easier to push through the die.
Key Characteristics of Hot Feed Extrusion:
- The rubber is pre-masticated (softened), reducing the energy needed during the extrusion process.
- Best suited for simple profiles and larger sections.
- Runs at slower speeds compared to cold feed extrusion.
- Uses higher temperatures throughout the process.
Advantages of Hot Feed Extrusion:
- Cost-Effective for Large Profiles: The process is ideal for bulkier extrusions, including rubber sections that require less complex geometries.
Enhanced Control: Hot feed extrusion offers excellent control over profile thickness and density. - Short Runs: Suitable for low-volume production, making it cost-effective for bespoke requirements.
Applications of Hot Feed Extrusion:
- Large Rubber Profiles: Thick fenders, buffers, or bumpers for marine and construction industries.
- Non-Reinforced Hoses: Basic rubber hoses that donβt require intricate reinforcement.
- Simple Gaskets and Seals: General-purpose sealing solutions.
At Harltex, our 200mm hot feed extruder allows us to handle large-scale profiles with precision, offering tailored solutions for industries requiring robust, heavy-duty components.
Cold Feed Rubber Extrusion
Cold feed extrusion involves feeding rubber compounds at ambient or room temperature into the extruder. This process relies on the extruder screw to soften and mix the rubber, eliminating the need for pre-heating.
Key Characteristics of Cold Feed Extrusion:
- Rubber is fed directly into the extruder at room temperature.
- More energy is required during the extrusion process to soften and push the rubber through the die.
- Runs at higher speeds compared to hot feed extrusion.
- Ideal for complex profiles and precision applications.
Advantages of Cold Feed Extrusion:
- Energy Efficient: Eliminates pre-heating, reducing energy consumption.
- Precision and Consistency: Excellent for creating complex profiles with tight tolerances.
- High-Volume Production: Runs at higher speeds, making it perfect for large-scale manufacturing.
- Material Versatility: Suitable for a wider range of rubber compounds, including
– FKM
– EPDM
– Natural Rubber
– AEM
– NBR
Applications of Cold Feed Extrusion:
- Seals and Gaskets: Precision extrusions for industrial machinery and marine environments.
- Tubing and Hoses: Rubber hoses for automotive, off-highway, and utilities industries.
- Protective Rubber Profiles: Edge trims, buffers, and profiles for health and safety applications.
- Complex Shapes: Intricate designs requiring accuracy, such as weatherstrips or custom profiles.
At Harltex, our cold feed extrudersβavailable in 60mm, 90mm, and 120mmβenable us to produce intricate profiles with exceptional precision and consistency.
Hot Feed vs. Cold Feed: Which Should You Choose?
The choice between hot feed and cold feed rubber extrusion depends largely on your application requirements:
Parameter | Hot Feed | Cold Feed |
---|---|---|
Pre-heating | Required | Not required |
Profile complexity | Simple profiles, larger sections | Complex shapes, intricate profiles |
Production volume | Short runs, low volumes | Medium to high volume production |
Energy efficiency | Moderate | High |
Applications | Large rubber profiles, basic hoses | Seals, gaskets, precision profiles |
The latest news from Harltex
πππ₯πππ«πππ’π§π 40 ππππ«π¬ of Harltex
This year marks a major milestone for Harltex Ltd β 40 years of precision-engineered rubber mouldings, extrusions, and bonded products, evolving with the industry, and pushing the boundaries of whatβs possible.
Why Choose Harltex for Rubber Extrusion?
At Harltex, we combine decades of experience with cutting-edge technology to deliver rubber extrusion solutions that meet the most demanding specifications. . .
Harltex Achieves WRAS Certification
We are proud to announce that our range of clean EPDM rubber materials have officially achieved WRASΒ certification...